How a 5-Axis Vertical Machining Center Outperformed Horizontal Machines and Boosted Efficiency
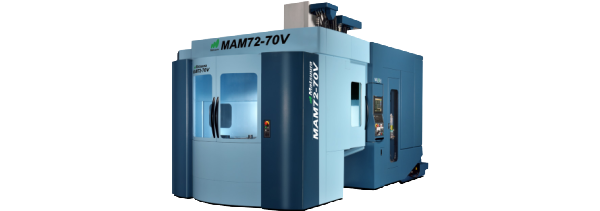
Problem/Need:
A customer was in the market for a large horizontal machining center to mill electronic housings that had a lot of internal features but was running into issues finding a solution that could keep up with the monthly quantity requirements.
Solution:
Since the customer was adamant about purchasing a horizontal machining center due to the large amount of material removal needed to produce the housing, we simply explored the available Matsuura horizontal machining centers at first. However, we quickly realized the customer would have to purchase multiple machines to keep up with the contractual monthly quantities demanded of them. This was out of the question due to floor space restrictions and budget constraints. We asked for a chance to review the part prints to see what other options were available. Our Applications team laid out the part parts in a variety of machines and started getting creative with work holding. Ultimately, our Applications team determined that not only did part fit perfectly in a the work envelope of a MAM72-70V, 5-axis vertical machining center, but they could vertically affix two parts, back to back, on a tombstone which would match the amount of parts per pallet (2) as the horizontal machine the customer originally was in search of. Additionally, the MAM72-70V was able to be configured with a 6 pallet retro-fit option that would gave them the ability to run “lights out” during off shifts which enabled them to produce enough parts to meet demands and also stay close to their budget.
Result:
In the end, our customer’s eyes were opened to the benefit of a large vertical 5-axis machine that, with a high-pressure coolant through spindle, was able to compete with a horizontal machining center in overall chip removal. The MAM72-70V was even able to reach and mill all the intricate features the horizontal couldn't in one operation and even perform a lot of finishing work within the machine. This was an even bigger benefit since it helped clear up their biggest bottle neck on the manufacturing floor, which happened to be their deburring department.